Casting aluminum components
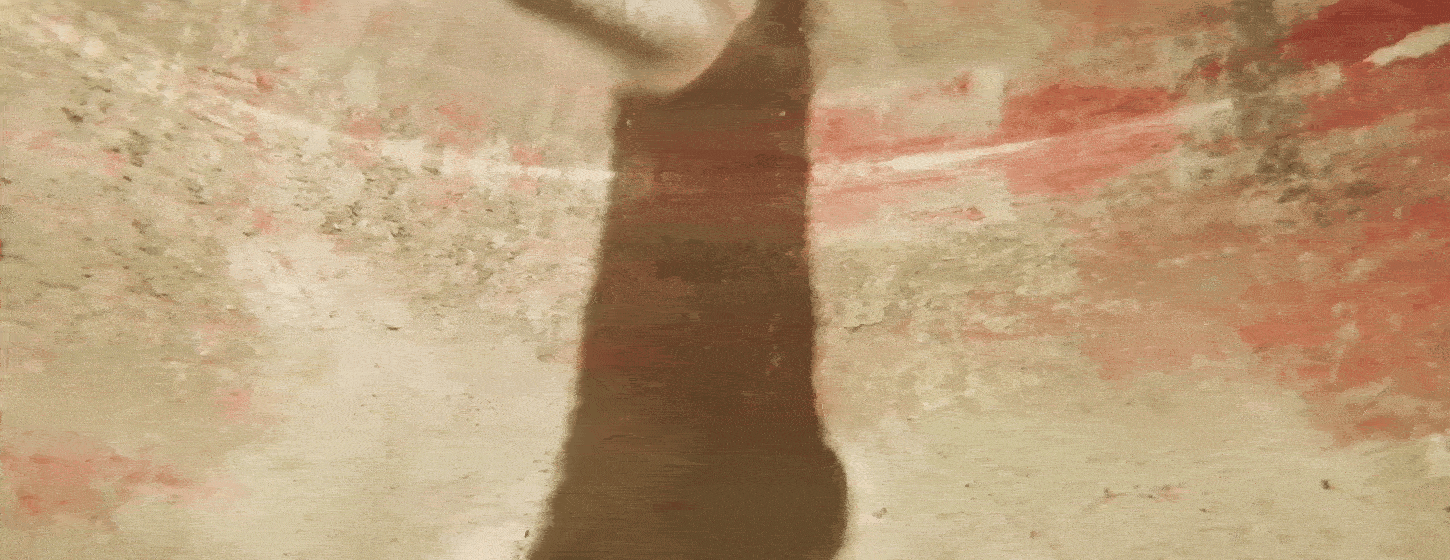
This is something I did back in 2018 when I got my first 3D printer, and I wanted to test if it was possible to fabricate parts out of aluminum. The idea was to use the printer to make a part out of cheap plastic, use it to mold a sand cast, and melt aluminum to pour in the cast, this would allow to self-fabricate parts out of stronger materials than plastic.
What i found out
Before choosing a complex part to test this process, I decided to try and print a knife blade (useless if made out of aluminum but with a simple enough shape) to learn how to work with aluminum, since I had no experience with that material. The first step was to build something that could both reach up to and withstand temperatures of around 660°C (the melting point of aluminum) while at the same time being as cheap as possible. My incredibly janky setup was therefore this: a steel bucket with a layer of refractory and heat-resistant cement inside. It wasn’t pretty, but it was effective and cheap. I then drilled a hole on the side to create an intake of air that was forced inside by a cheap hairdryer, this provided the coal placed in the forge with oxygen and allowed it to burn at much higher temperatures than normal. A simple lid made out of cement was used to avoid heat dispersion, and the receptacle I used was a steel saucepan since I knew I wouldn’t go as hot as steel’s melting temperature (around 1400 °C).
I first started taking apart some old car engines I recovered at a scrapyard to make them fit the small receptacle. The first step was to melt them and cast some ingots to hopefully remove any impurities. I built the forge, filled it with coal, and lit the fire. Using an infrared thermometer, I verified that the temperature shot up to around 800°C after turning on the hairdryer and getting it ready to accept the first pieces. I watched as they quickly melted and prepared a batch of wet sand to cast the aluminum into.
After removing some of the slag that floated to the surface, I cast it into the sand and quenched the resulting ingots in water. This way, I would hopefully get some high-quality ingots I could use for future castings.
Once I had some good-quality aluminum ingots, I started the process of melting again. This time, I wanted to try the true process of casting, where two sand molds are created and the casting is done between them. I prepared the two halves of the cast, leaving some vertical channels to pour the aluminum and let the air escape.
And proceeded to pour.
I then spent the next few hours polishing and detailing the knife until I was satisfied. The result wasn’t too bad, but during the process, I realized that with the equipment I had, it would have been basically impossible to get precise shapes, the sand casts I used weren’t ideal, and a lot of the sand crumbled when entering contact with the molten aluminum. On top of that, while coal was the safest and easiest to source fuel to get to those temperatures, it turned out to be quite expensive after a while, the forge burned about half a kilogram of it per minute.
While the original intent of making complex parts out of aluminum turned out to be just a bit out of my reach, the whole process was incredibly fun, and I learned a lot while doing it. Plus, plus, I got a pretty sick (terrible for cutting) knife out of it!